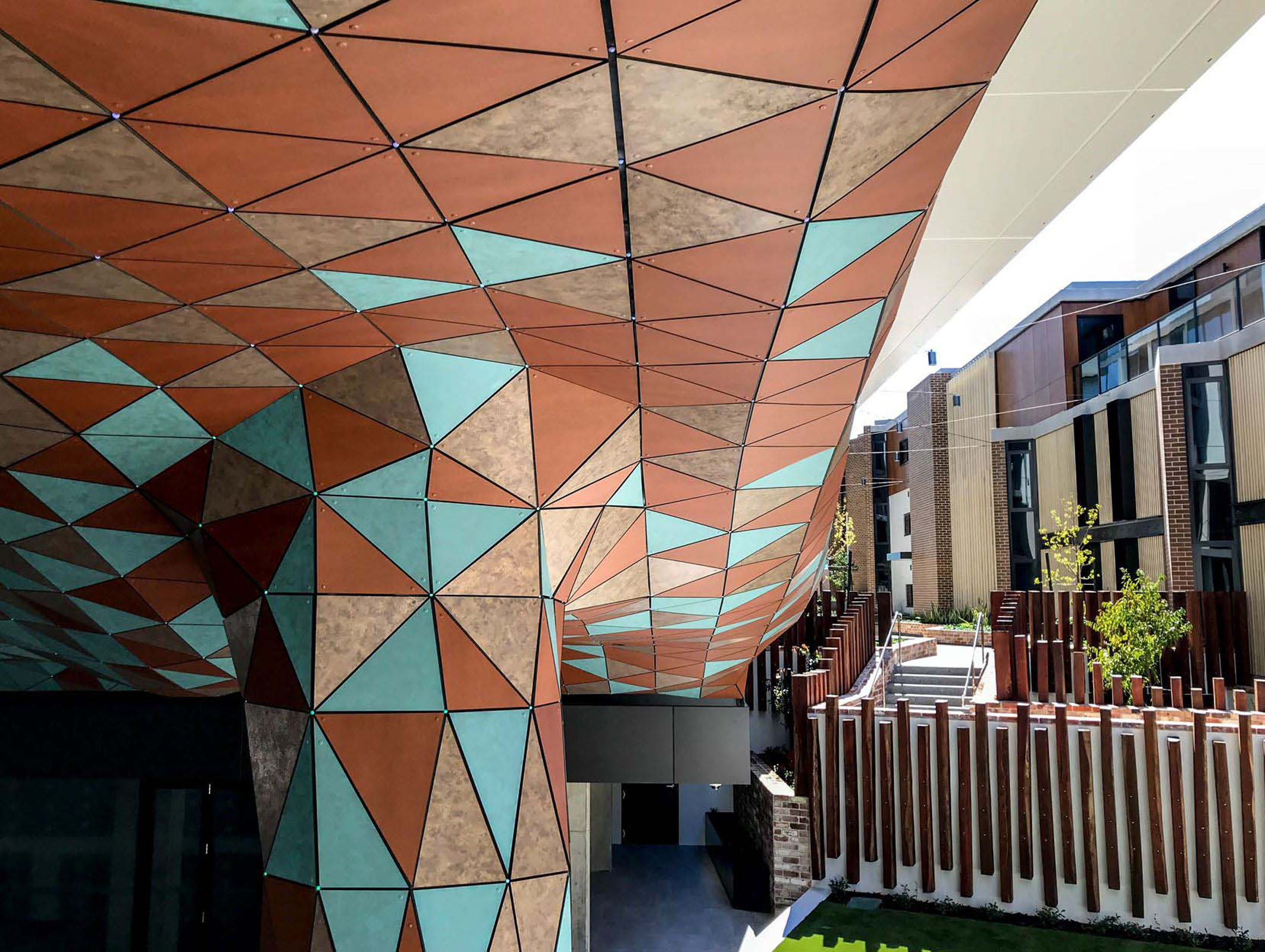
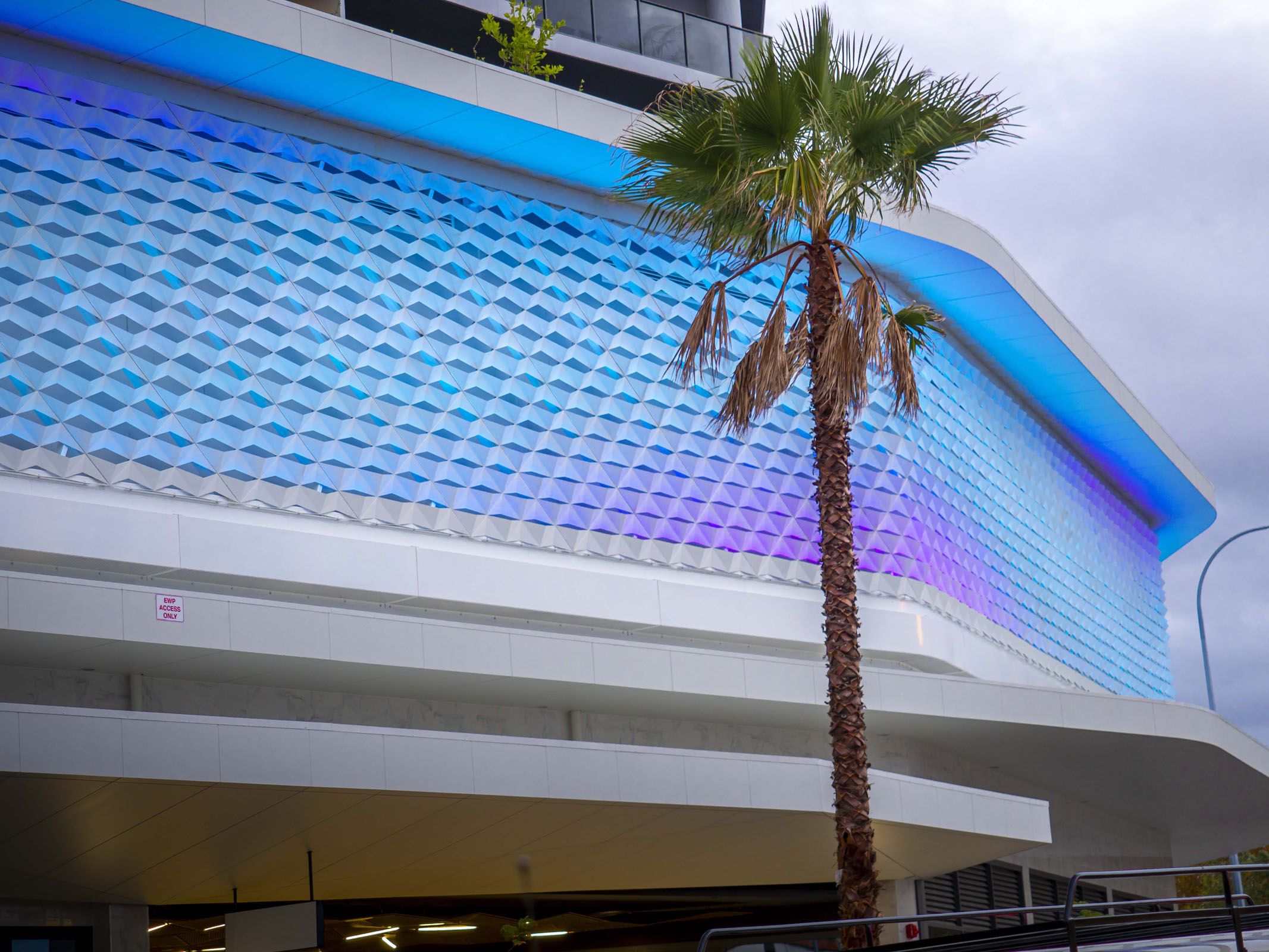
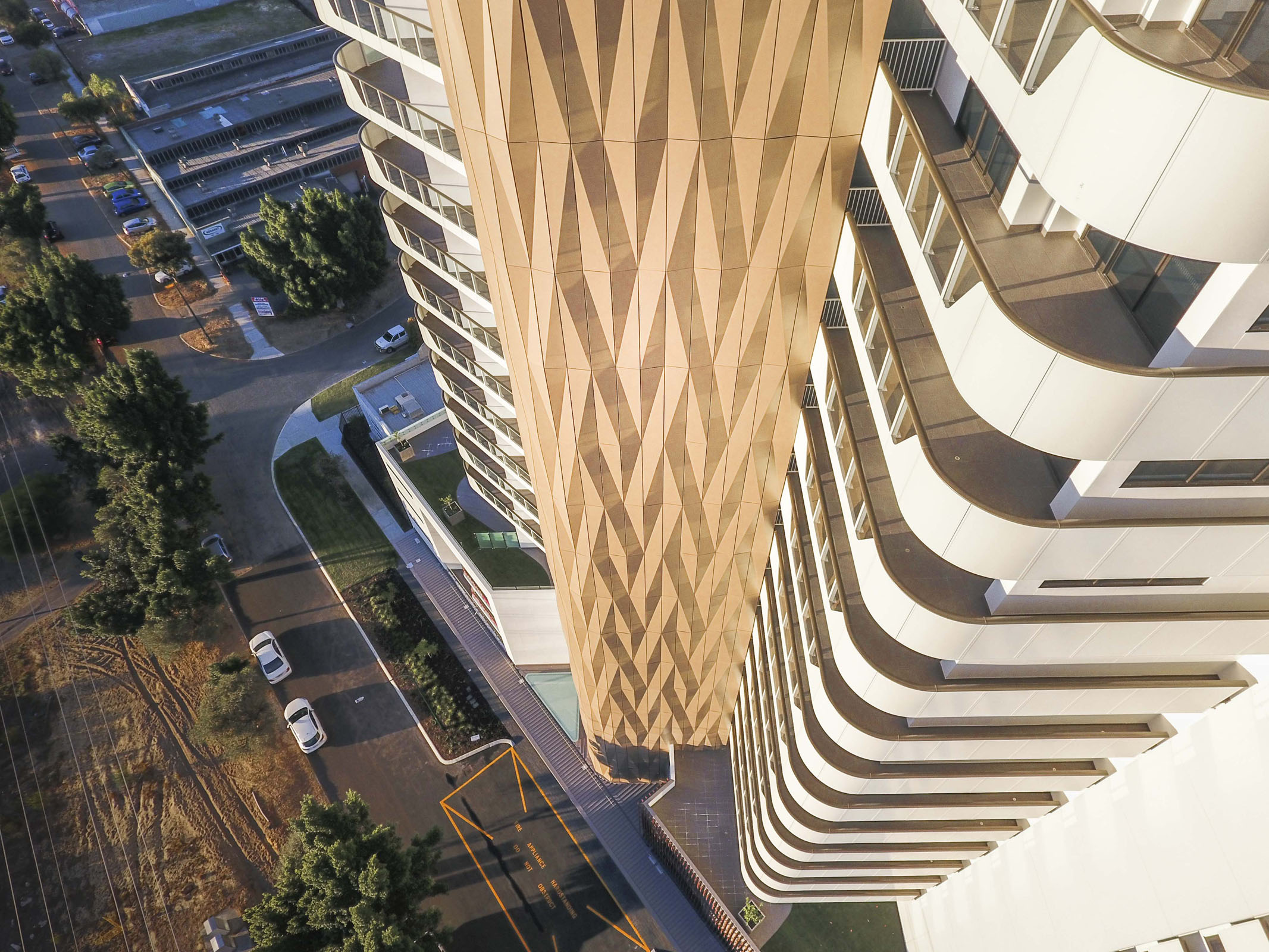
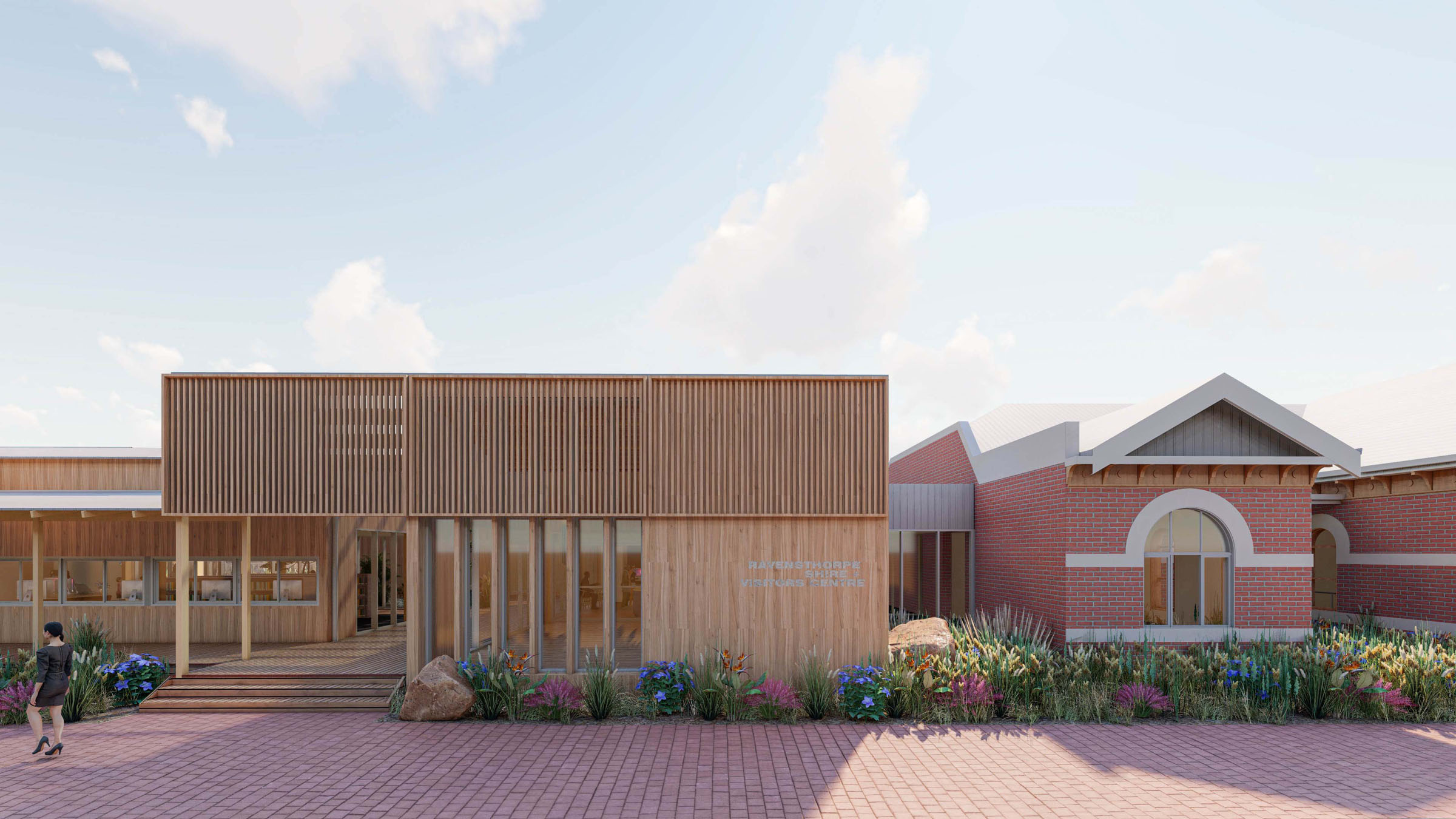
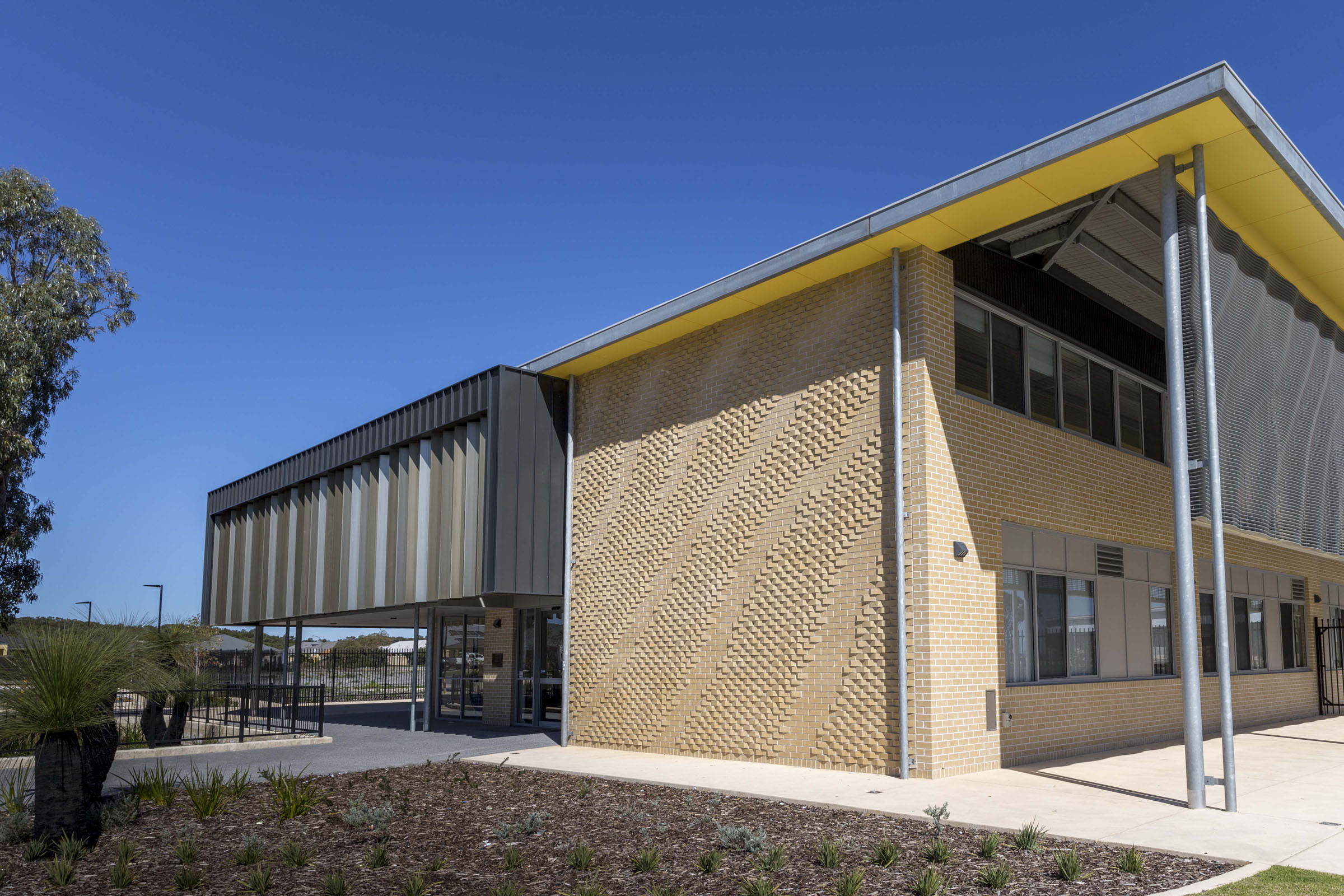
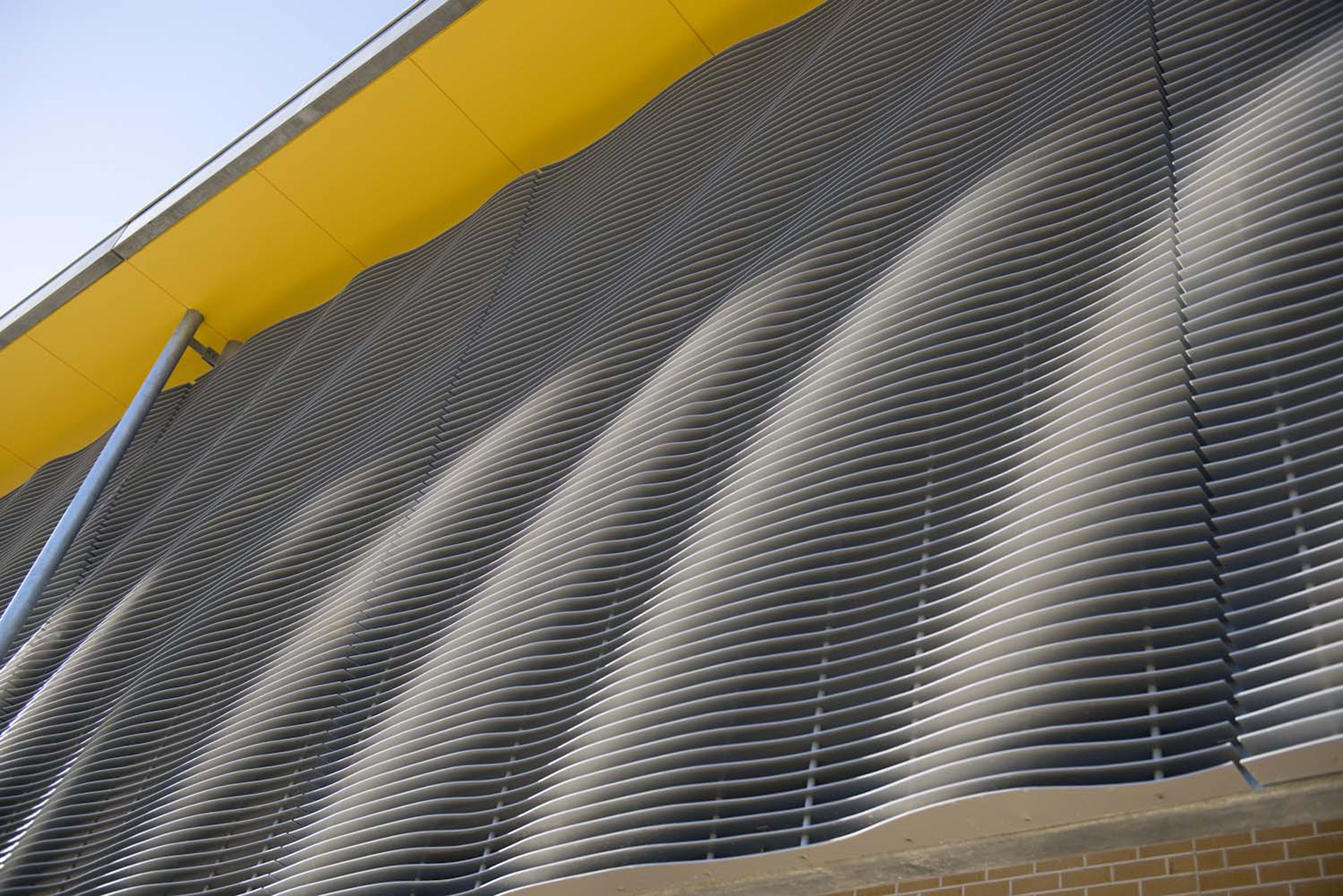
Intensive Fields is a transdisciplinary design practice based in Western Australia. We combine human-centric design with advanced technology and techniques to deliver projects and spaces that are inclusive, equitable, sustainable, and resilient. We work closely in collaboration with our clients and communities, ensuring the optimal balance of quality, cost, and impact.