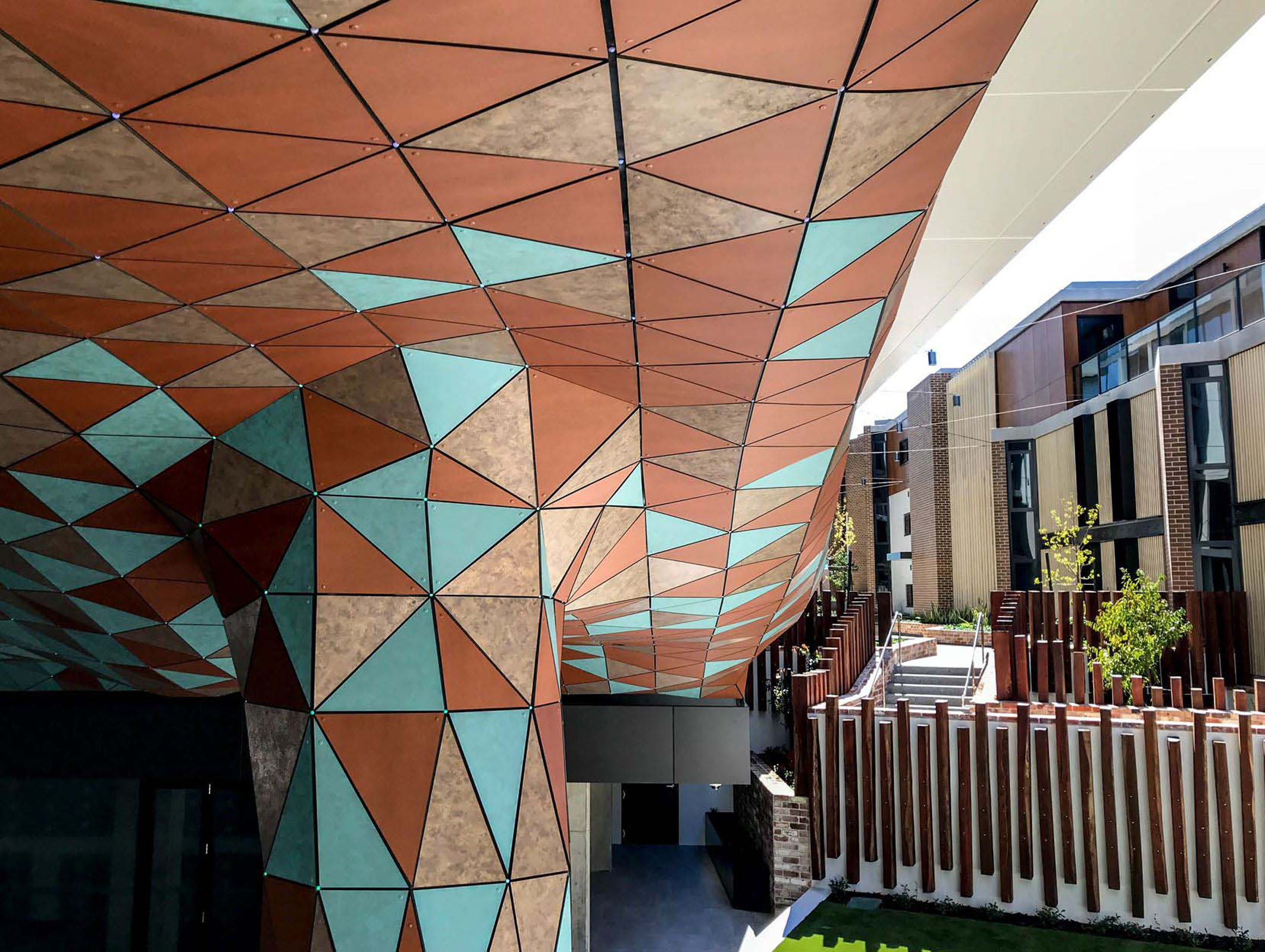
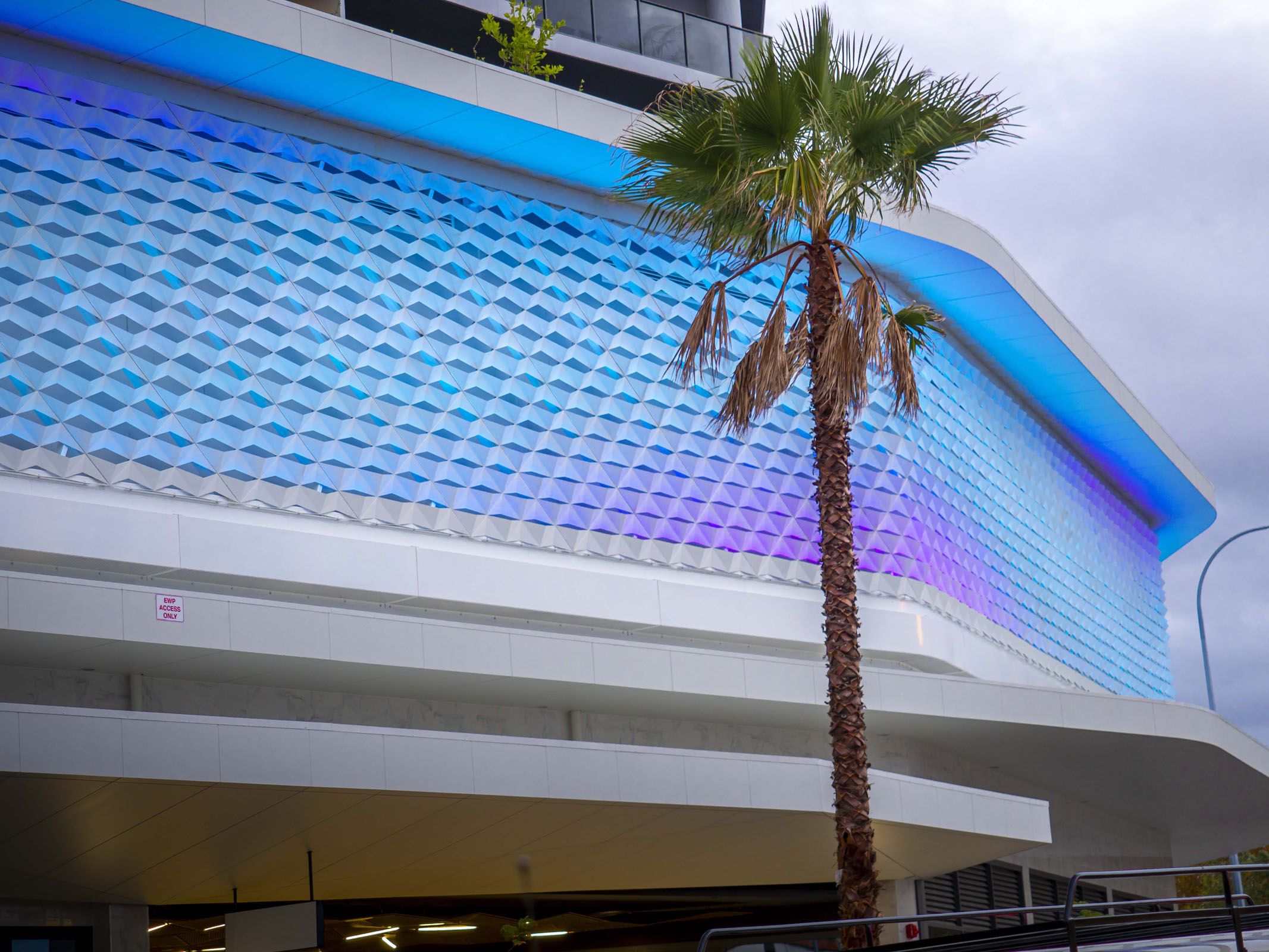
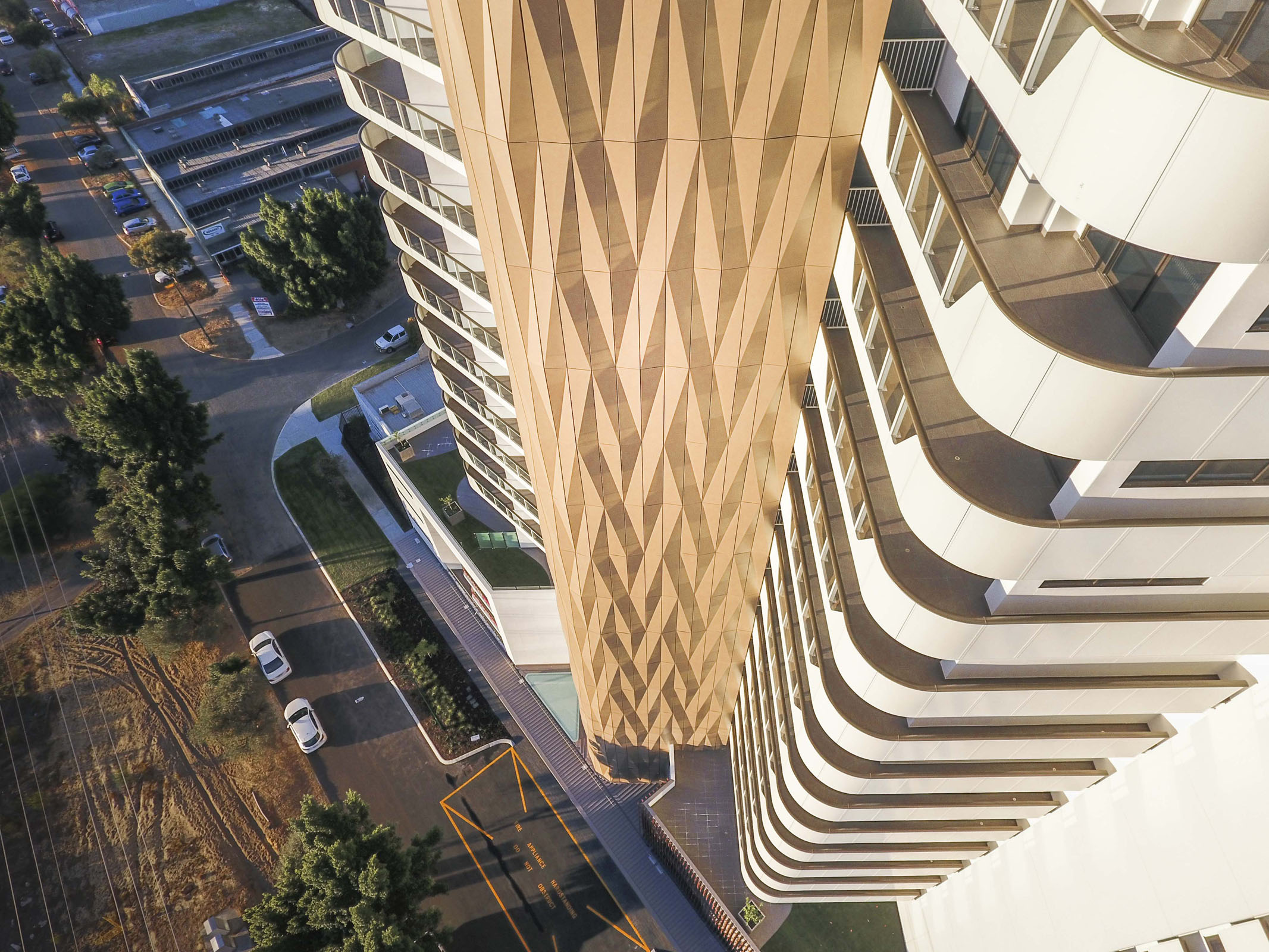
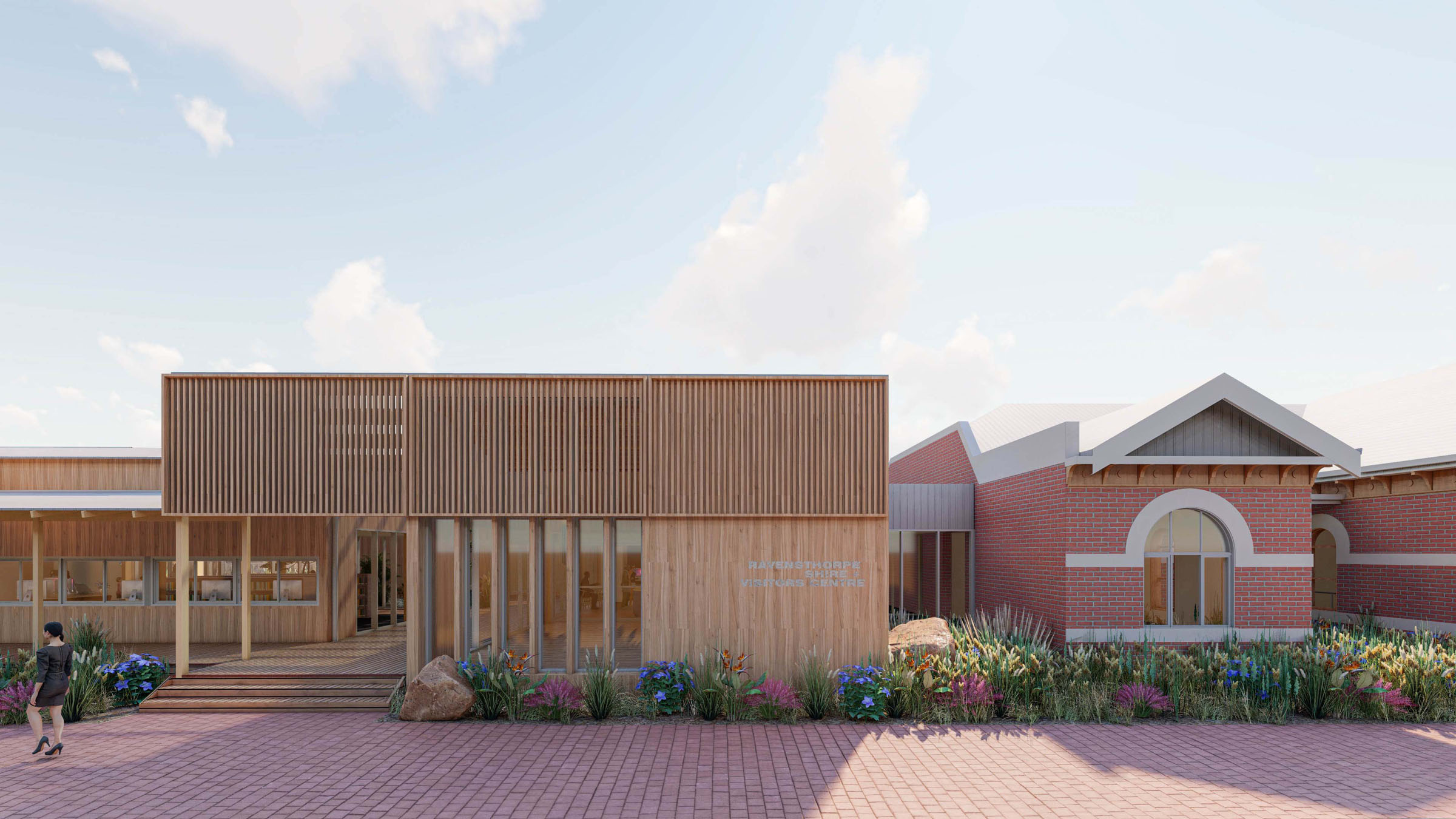
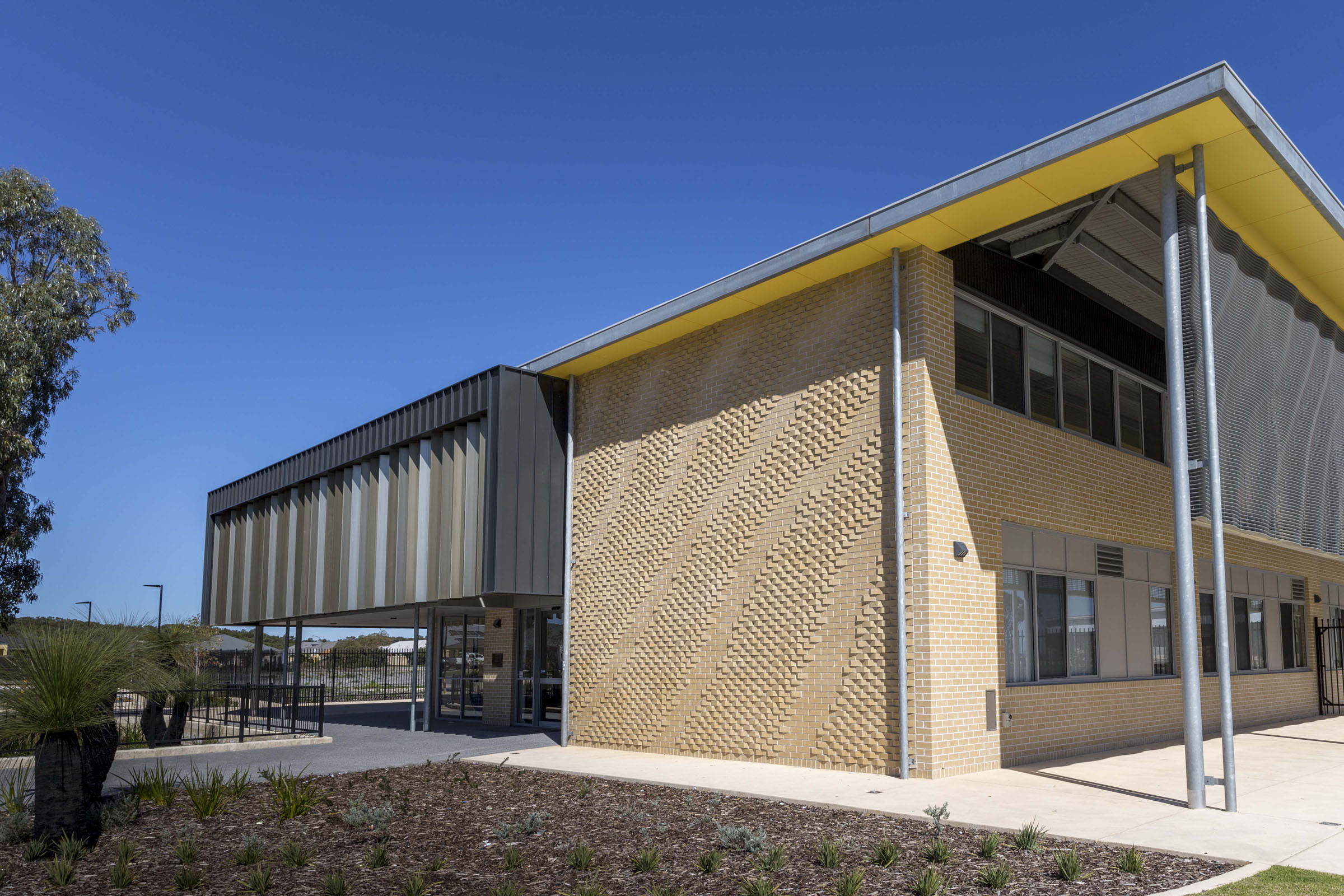
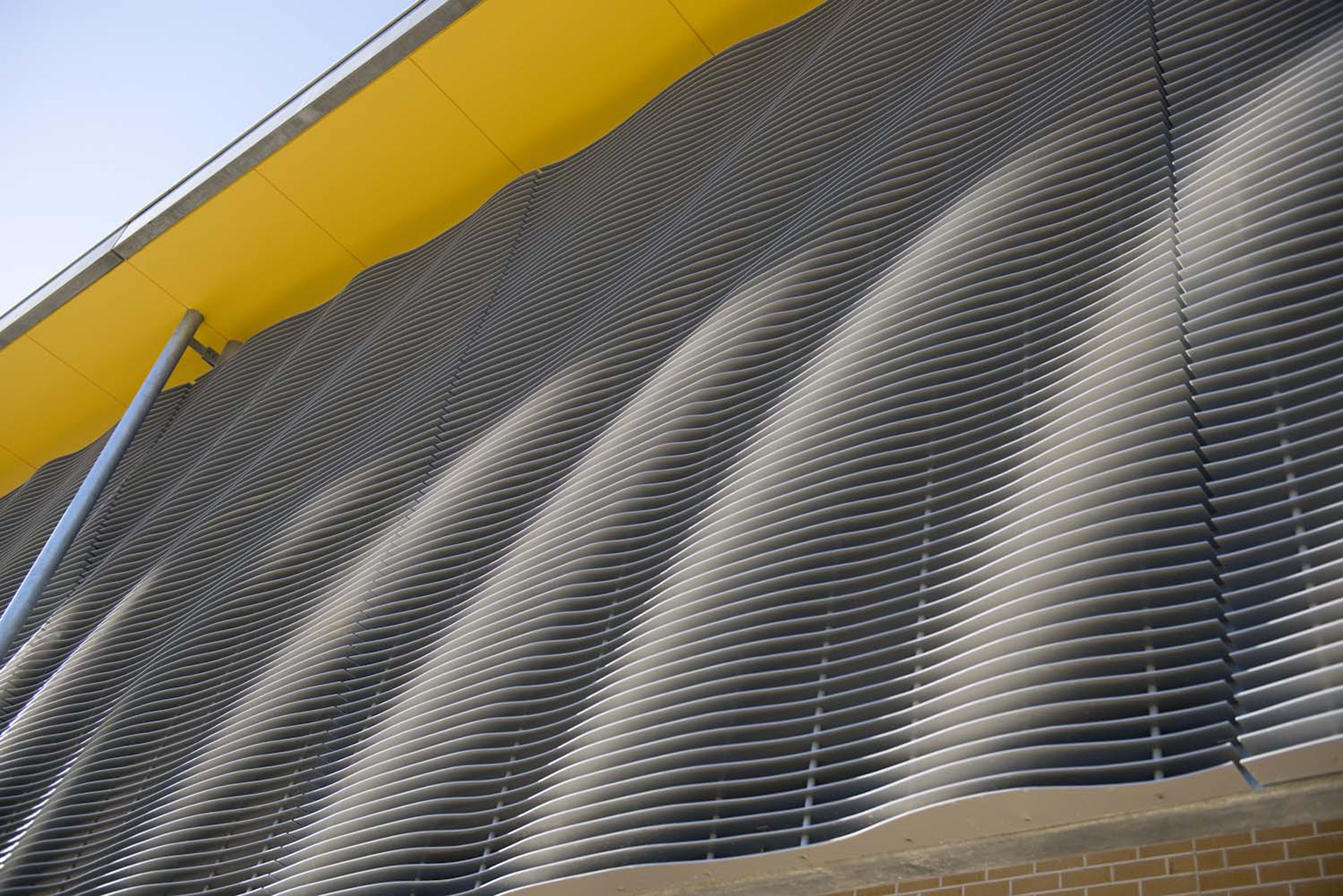
We ask What if we could change the future by changing building?
We are IMPACTFUL.
- Acknowledging the potential for positive change through design.
We are ETHICAL.
- Design for good and access for all.
We are DEFIANT.
- Challenging the status quo and always searching for a better process and outcome.
Let us help change the way you build
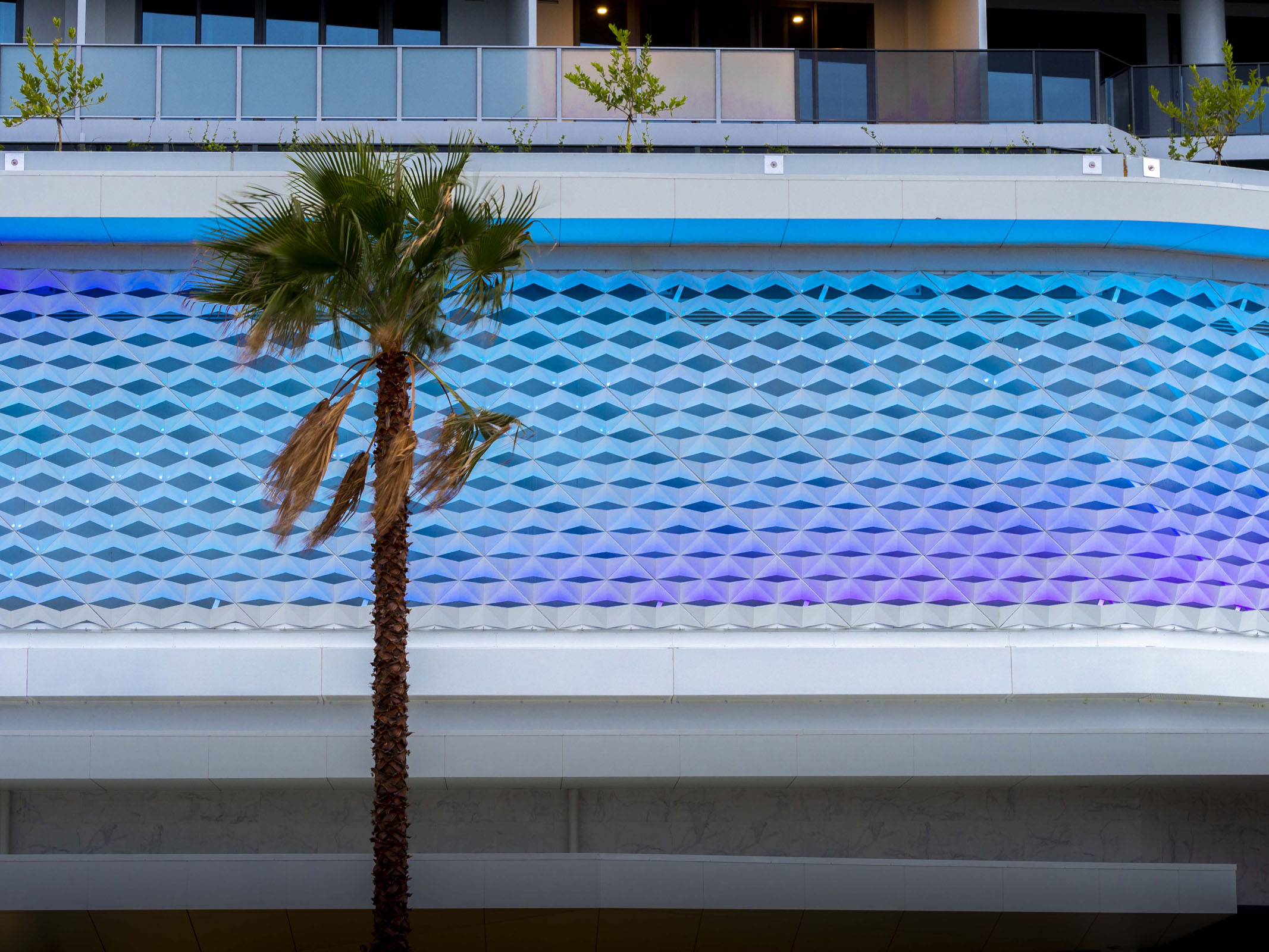
Contact Us
About Your Project
if/LAB is a transdisciplinary design and technology studio based in Perth, Western Australia.
We leverage innovation in design, technology, and manufacturing to enable equitable access to better design for all.